Project background
In an inertial navigation system, gyroscopes and accelerometers are the core components of the system. The working accuracy, reliability and stability of gyroscopes and accelerometers are one of the important factors that determine the accuracy, reliability and stability of inertial navigation systems. As the application fields of inertial navigation systems continue to expand, the environment in which they are used becomes increasingly harsh. To ensure reliable and stable operation in various harsh environments, it is necessary to compensate for changes in various environments. Among various environmental factors, temperature drift is the main error source of inertial devices. Therefore, the research on temperature error measurement and compensation technology of gyroscopes and accelerometers is one of the hot topics in current inertial navigation technology research.
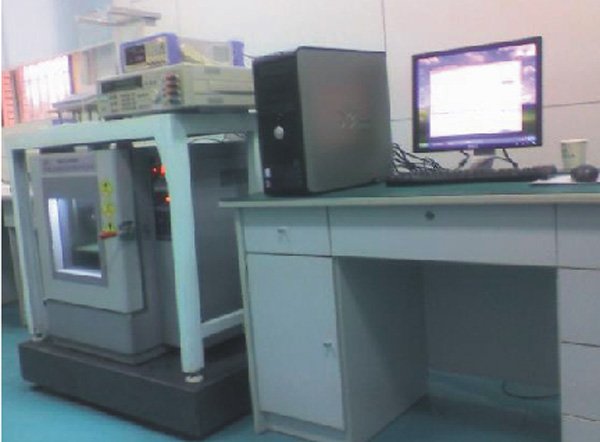
Needs analysis
For dynamically tuned gyroscopes and quartz flexible accelerometers, the influence of temperature on device accuracy is mainly manifested in the deformation of the device caused by thermal expansion and cold contraction, which causes axial deviation of the center of mass of the rotor body, radial imbalance, unequal elasticity, and various internal factors of the torque device. Changes in physical parameters of materials, etc. Among the above influences, changes in the physical parameters of the materials inside the torque converter (mainly the temperature coefficients of permanent magnet magnetic materials and soft magnetic materials) play a dominant role. Therefore, measuring and compensating the torquer temperature coefficient has become a key factor in improving the performance of dynamically tuned gyroscopes and quartz flexure accelerometers.
Measurement principle
The change of the gap magnetic field is measured by measuring the change of the energized coil force in the gap magnetic field, thereby calculating the temperature coefficient.
The test system is designed based on the force effect of current in the magnetic field. In the magnetic field, F=BIL, there is a linear relationship between the force and the magnetic induction intensity of the magnetic field. Then measuring the force generated by the conductor in the magnetic field can calculate the size of the magnetic field. The accuracy of magnetic field measurements depends on the current, wire length, and force. When B and L are constant, F is proportional to B. That is B=KF. If the corresponding stresses F1 and F2 at temperatures T1 and T2 are measured respectively, the temperature coefficient can be expressed by the following formula α=(B2-B1)/(T2-T1)/B1=(F2-F1)/(T2-T1)/ F1.
Solution
A high-stable constant current source is used to ensure the stability of the test coil current. A high-precision analytical balance detects changes in electromagnetic force. The thermistor measures temperature changes. The relationship between magnetic field changes and temperature can be accurately obtained. All data are automatically read into the computer. After data processing The temperature coefficient at different temperatures can be measured.
System structure
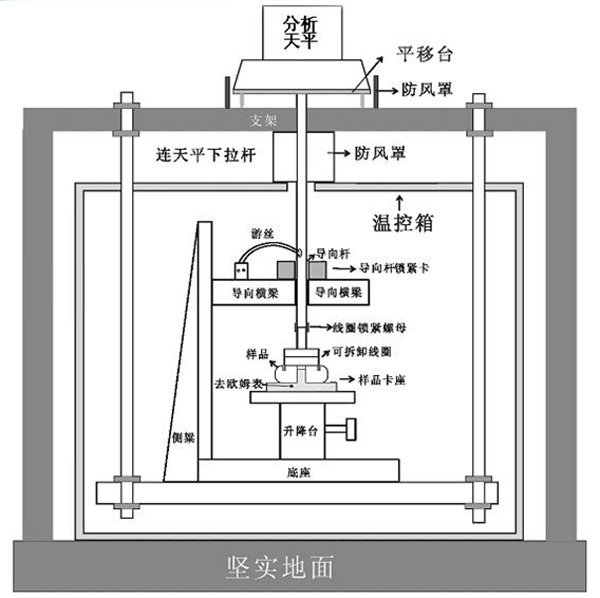
Technical parameters
Test gap magnetic field temperature coefficient resolution: 1×10-5
Measuring temperature range: -40℃-100℃;
Temperature display resolution: 0.1℃;
Meets different structural tests of torque converters;
Repeatability of test data: including the second installation of the card and the second startup, the significant figures of the measurement value are ±5×10-2: if the average measurement value is 4×10-4/℃, the repeated measurement value is (3.8-4.2) Between ×10-4/℃.
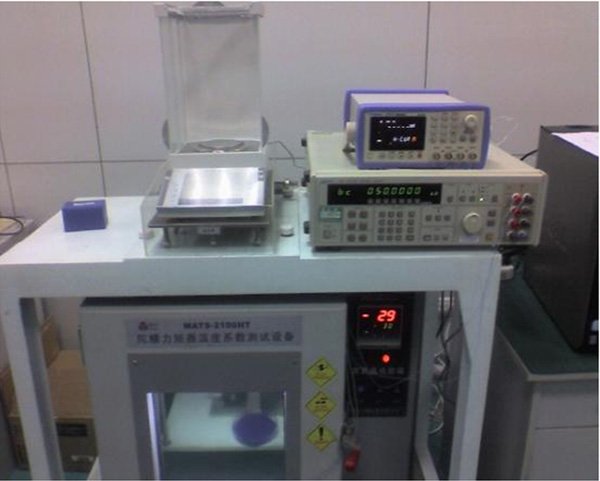
Software interface
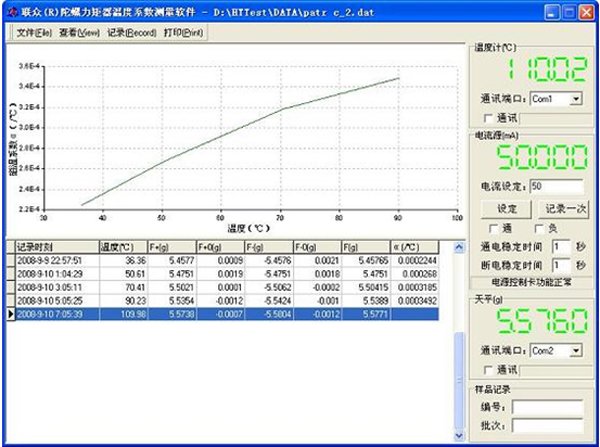